What Does Vinyl Ester Resin Mean?
Vinyl ester resins are thermosetting matrix resins that can be considered a hybrid of epoxies and polyesters. It is a molecular chain composed of several ester groups double-bonded to vinyl groups, which differs from polyester in the position of the reactive sites. It is made by the esterification of epoxy resin and unsaturated monocarboxylic acid. Vinyl ester resin is used in transportation, construction, infrastructure, military, energy, and marine applications (piping, composites, storage tanks).
Vinylester has a long molecular chain, so the resin is strong and elastic, and absorbs impact. It is resistant to water and chemical reactions due to its hydrolytically susceptible ester group. When vinylester is used in laminations, additives are required to speed up the curing process and impart corrosion resistance.
What Is Vinyl Ester Resin Used For?
Vinylester is Used in a wide variety of markets today, EVER is highly durable and combines the toughness of epoxies with the ease of processing and low-temperature curing of polyesters. Vinyl ester resins are used in demanding applications such as corrosion-resistant industrial tanks and pipes and pultruded profiles. Additionally, Vinyl ester resins are widely used in critical automotive and marine components. Boost your performance with our epoxy vinyl ester solutions. PVC Resin is not a good option for these applications.
Vinyl Ester Resin Properties
Epoxy vinyl ester resins (VER), often abbreviated as vinylesters, are an important class of high-performance thermosetting molding compounds. They are produced by adding an α,β-unsaturated carboxylic acid to an epoxy resin. The two main types of epoxy resins are bisphenol A diglycidyl ether (DGEBA) and epoxy phenol novolak (EPN). These resins form durable laminates and coatings when fully cured (crosslinked). Their performance is often intermediate between conventional unsaturated polyesters and epoxy resins.
The properties of the cured vinyl resin depend on the type of epoxy and vinyl monomers (reactive diluents) used and their relative amounts. The majority of commercial vinyl polyester resins are derived from bisphenol A diglycidyl ether (DGEBA) as the epoxy component and acrylic or methacrylic acid as the vinyl monomers in the polymer. Many other epoxides and vinyl acids or esters can be used to tailor the properties of unsaturated polyesters. For example, (modified) novolac epoxies are sometimes chosen for their better heat and chemical resistance, while dimer fatty acid glycidyl methacrylate-modified resins are more flexible but less chemically resistant. durability and heat resistance are reduced.
Vinyl ester resins are relatively viscous, low molecular weight prepolymers. To make them more processable, they are usually dissolved in a vinyl monomer (sometimes solvent 1) along with a suitable organic peroxide The mixture is poured, sprayed, or molded into the final product. Many Vinyl resins can also be cured at room temperature if a reducing agent such as cobalt naphthenate or cobalt octanoate or an aromatic tertiary amine is added to the system. increase. This compound is often called an accelerator or activator. PVC Resin products with activators are typically two-component systems, while thermosetting Vinyl ester resins are typically one-component systems. Cure and pot life depend on the initiator system, its concentration, type of resin and vinyl monomer, and cure temperature.
The most common vinyl monomer is styrene. It acts as a reactive diluent and crosslinker. When polymerized in the presence of unsaturated polyesters, it reacts with the double bonds of the prepolymer but also homopolymerizes. The degree of homopolymerization and copolymerization depends on the reaction conditions, monomer content, and miscibility of the two resins.
Due to growing health concerns3, the styrene content of many resin systems has been significantly reduced or replaced with less toxic vinyl monomers such as vinyl toluene, vinyl acetate, methyl (meth)acrylate, and diacrylates and It has been completely replaced by difunctional vinyl monomers such as diacrylates. Dimethacrylate. The nature of the reactive diluent affects both the cure and final properties of the polyester.
Some Vinyl ester resins can also be chemically modified to achieve practical viscosity without the addition of reactive diluents. For example, the viscosity of the resin is greatly reduced by the reaction of the secondary hydroxyl groups of the epoxy moieties with diisocyanates.
Vinyl Ester Resin Features And Application
Vinyl Ester resins are specially formulated vinyl esters with excellent resistance to a wide range of corrosive chemical environments at room and elevated temperatures. It is based on selective epoxies and methacrylic acids that have been carefully processed to specific molecular weights, dissolved in styrene monomer in the presence of specially selected inhibitors, and have shelf lives of several months or more. Unpromoted, non-thixotropic formulated chemically stable unsaturated polyester resin @ room temperature. Vinyl ester resin is resistant to chemicals/fluids for a wide variety of exposures and applications. This vinyl resin is particularly suitable for chemical process equipment such as filament windings, lay-up/spray-up, pultrusion tubes, reactors, fans, fume control equipment, etc., and is resistant to a wide range of chemicals/fluids for exposure and application. Vinyl Resin plastics are majorly used in surface coating. Vinyl chloride Resin is used to make polyvinyl chloride (PVC) pipes, wire coatings, vehicle upholstery, and plastic kitchenware.
Typical Application:
- For manufacturing bridges, ladders, etc. that are exposed to harsh sewage and sewage.
Liquid state physical data at 250C# [approved to IS 6746-1994 and BS 3532-1990]
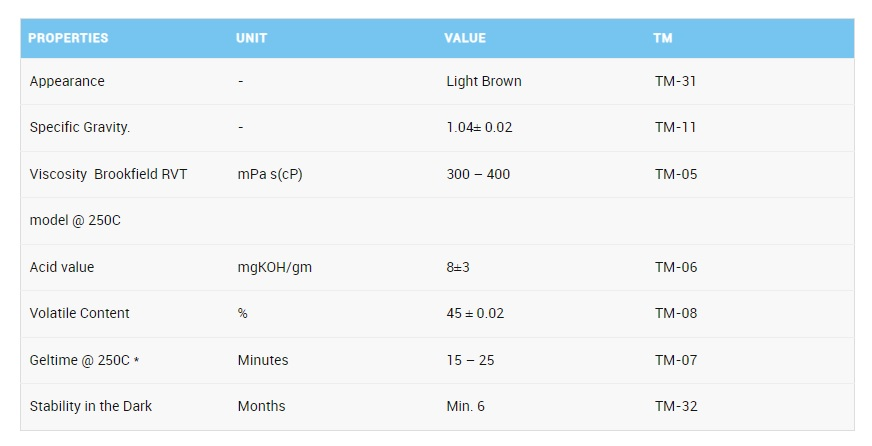
- Accelerator, Co (6%) 0.4 phr, Promoter (100%) DMA- 0.05 phr
Catalyst Butanox M50- 1.2 phr, measured gel time, cure time, and peak exotherm.
Properties of cast resin laminate (on base resin)
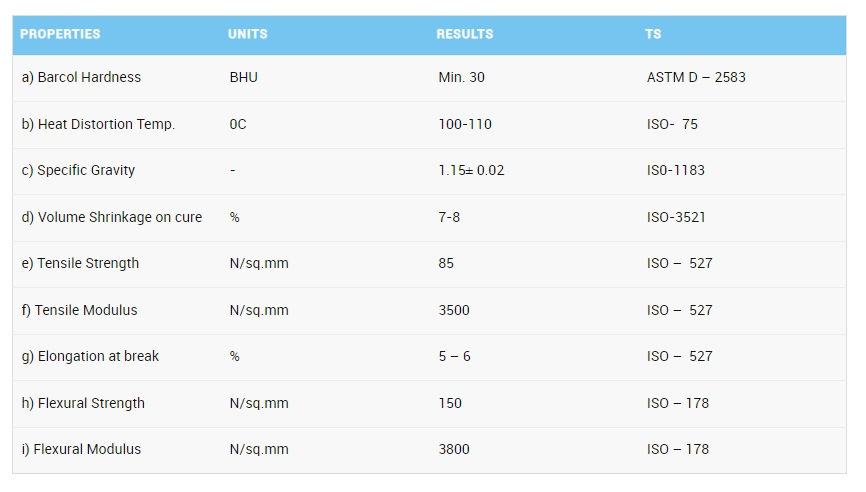
Post-Cure Laminate Tested TS – Test Criteria
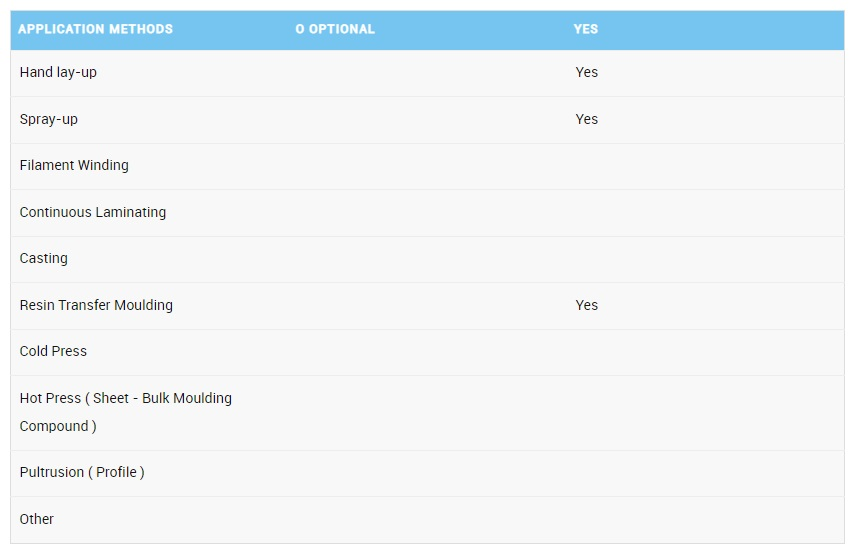
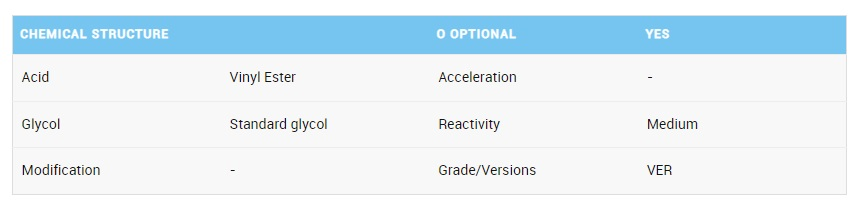
Technical Details Of Vinyl Ester Resin
The surface quality is not as good as polyester. The built-in toughness of vinyl ester resins makes it difficult to achieve smooth surfaces. Double bonds cause shrinkage and adversely affect surface quality.
The double-bonded vinylester groups give the overall matrix approximately twice the toughness of polyester, depending on the test used. For example, typical tensile properties of SMC start at around 15,000 psi, and with 28% glass reinforcement, flexural properties exceed 30,000 psi. Vinylester, like polyesters, is impractical without additives, reinforcements, and fillers. The next step towards toughness would be polyurethane or epoxy.
Like polyester, it has a very good strength-to-weight ratio and a low density (approximately 1.80 grams/cm³), so it often replaces metal parts that are nearly five times heavier.
The modulus (stiffness) is slightly lower than and comparable to polyester due to the toughness built into the ester-linked backbone. The normal viscosity of vinyl esters is lower than that of polyesters, about 500 centipoises when cut into styrene monomer. Both polyester resins and vinyl resins react to increase their molecular weight to solid waxy resins, which are almost unusable in this waxy state. Therefore, when handling it as a liquid resin, it is common to cut it into styrene monomers.
Vinyl Ester Resin Usage & Post Curing
Vinylester works best when the laminate is fully post-cured. The amount of catalyst and accelerator can be adjusted to shorten or lengthen the gelling time. Vinylester is more tolerant of stretching than Vinyl Resin. This makes them more able to absorb impact without damage. We recommend aging the product for 24 hours and post-curing at 80ºC for at least 6 hours. This is recommended to get the best properties. Packaging: usually 35kg (carboy) 205 kg (drum/barrel)

Leave a Reply